Combine header offers high-productivity harvesting
14th June 2024
Agriculture is, and always will be, challenged by the weather. Whether drought or drowned, mother nature will dictate the cultivation of crops for many years to come. As weather windows seem to tighten and farm businesses are scaled up, there is a need to increase the productivity and efficiency of machinery to deliver a profitable harvest.
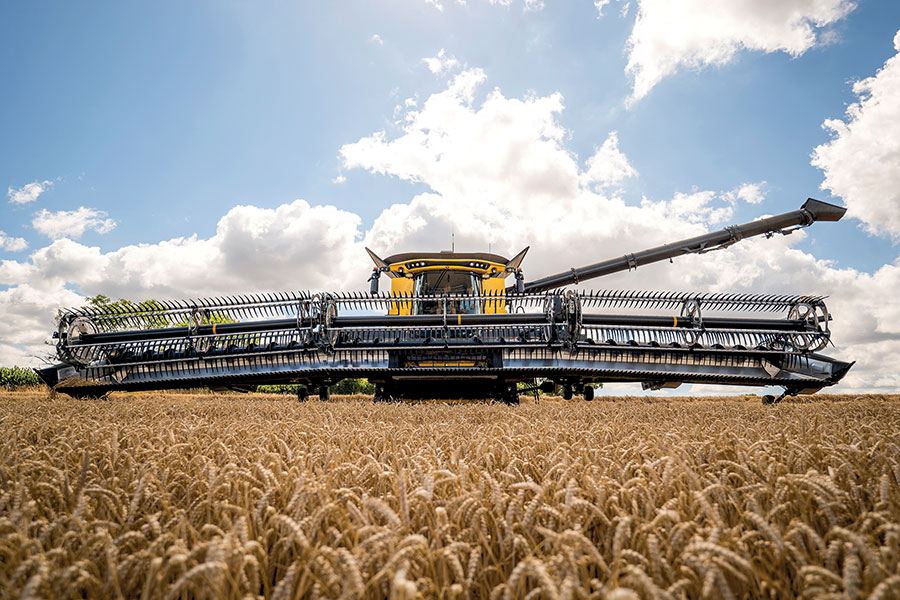
History of drapers
Turning the clocks back, even the earliest binders and harvesting machines used draper style feeding in the form of canvases for the benefits of heads-first feeding to the threshing unit. The practicality and maintenance of damp canvases though was one of the main causes of the shift towards auger headers. For smaller headers, the simple driveline and rigid frame provided a low-cost and functional approach to combine feeding.
Fast forward to 1986 with many technological advances in draper manufacturing and engineering, MacDon’s experience with swather draper headers generated demand to fit its rubber-belted swather header to combines. The cost and performance benefits of heads-first feeding were again realised and from there exploded the demand for combine draper headers in the American Midwest.
Multi-crop advantages
In a period of wet weather, drilling windows and harvest windows are shortened; both of which put pressure on the combine when it is most critically needed. Crop diversification is one solution to this challenge so long as the crop can be suitably harvested when ready.
The MacDon FD2 has been tested in practically every crop around the world, in pretty much every condition anyone would dare to put in front of it. In many scenarios, the combine header is known to be the limiting factor for combine throughput where lodged wheat or damp, dewy barley make for a very unpleasant harvesting experience. Having the draper feeding and the floating headstock make this significantly easier on the operator, giving the farm the confidence to plant a range of diverse crops and trusting that the header will not be the limiting factor at harvest time.
Floating linkage
The wet weather doesn’t just create pressure at drilling and harvest time though. The need to get fertiliser on early is notorious for leaving rutted tramlines which cause havoc with height-sensing combine headers at harvest. Having the header mounted on a floating linkage takes the stress out of navigating these, which MacDon says it has perfected since the release of the FlexDraper in 2004. The system works neatly in conjunction with the combine’s existing auto header height control system, but allows the combine to take a relaxed back-seat approach to ground following. The instant mechanical response means badger sets and tramline ruts are no longer a worry to the operator, and negate the downtime associated with changing knife sections.
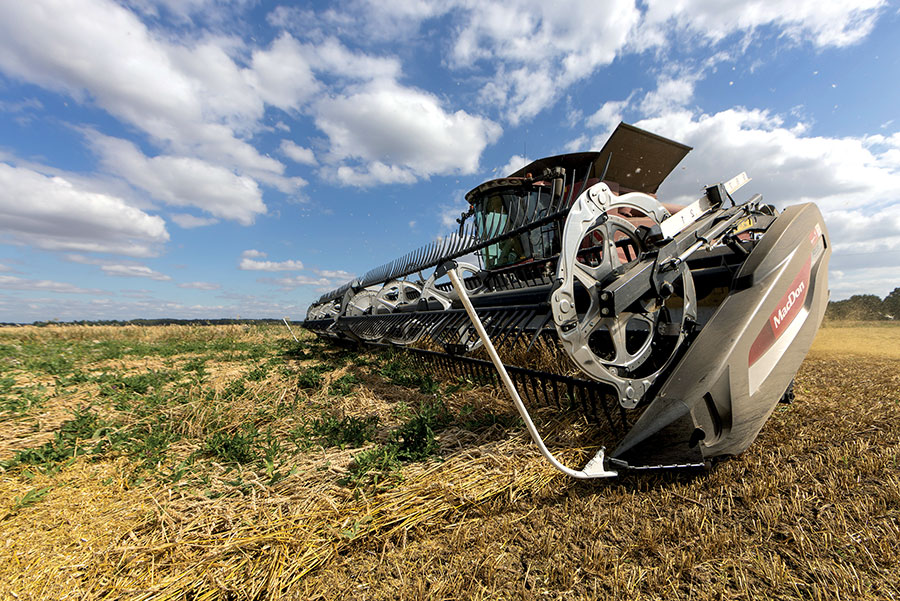
Along with the floating linkage, the frame of the FlexDraper is split into three sections. Each of these follow the ground independently, allowing the header to work much closer to the ground where laid crop or short crops are nestled in valley bottoms or over ridges in the field. While this capability was developed with the terraced fields of the Midwest in mind, it has just as equally found a new home in the rolling vales and hills of the UK. Being able to cut all the crop without the need to cut at multiple angles means reduced field passes and an easier operator experience.
Integration
Just as the three-point linkage and Isobus has standardised the tractor implement side of the industry, MacDon says it is leading the way with ensuring seamless compatibility between combines and combine headers. By interfacing through the existing combine’s controls, the MacDon FD2 retains the functionality and features that one could expect from a combine manufacturer’s own header.
Knowing that the header can be adapted to a range of combine brands allows farmers to invest knowing that the header can be kept for multiple combines, regardless of whether the combine colour changes down the line. Not many will look back to the days when a plough and tractor were bought as a combined unit; the practicalities and benefits associated with the commonised three-point linkage really set the bar for justifying capital expenditure, allowing tractor and implement manufacturers to innovate and specialise separately in their particular area.
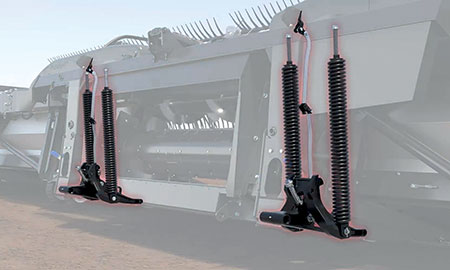
In an uncertain economic climate, there is a tendency to hold on to equipment longer and make purchases that have a more direct impact on business performance. While the FD2 will improve the productivity of the combine, the additional investment needs to be justified, the manufacturer acknowledges. The high serviceability and minimal regular maintenance of MacDon headers lends itself to a long service life, evidenced by many FlexDraper headers having done several thousands of hours. This longevity helps maintain the resale value and further reduces the cost of ownership. Retaining the header for multiple combines is a new concept to the European market but one that is firmly established in other markets, allowing equipment to earn its full potential rather than being traded prematurely.
The trend towards draper headers has been accelerated by the growth of farm businesses and the need to get more out of the combine at harvest. The MacDon FlexDraper has led the European charge in the shift to draper headers and continues to deliver on innovation and performance to ensure it can meet the demands of modern agriculture in challenging conditions.
Visit the MacDon website for more information
View FarmAds combine harvesters for sale