Growing awareness of the need for routine lifting machinery checks
9th July 2021
“There is greater awareness of the need for all lifting equipment to be tested regularly, to ensure it is safe to use,” explained Bickers Lifting general manager Steven Churchyard. “We
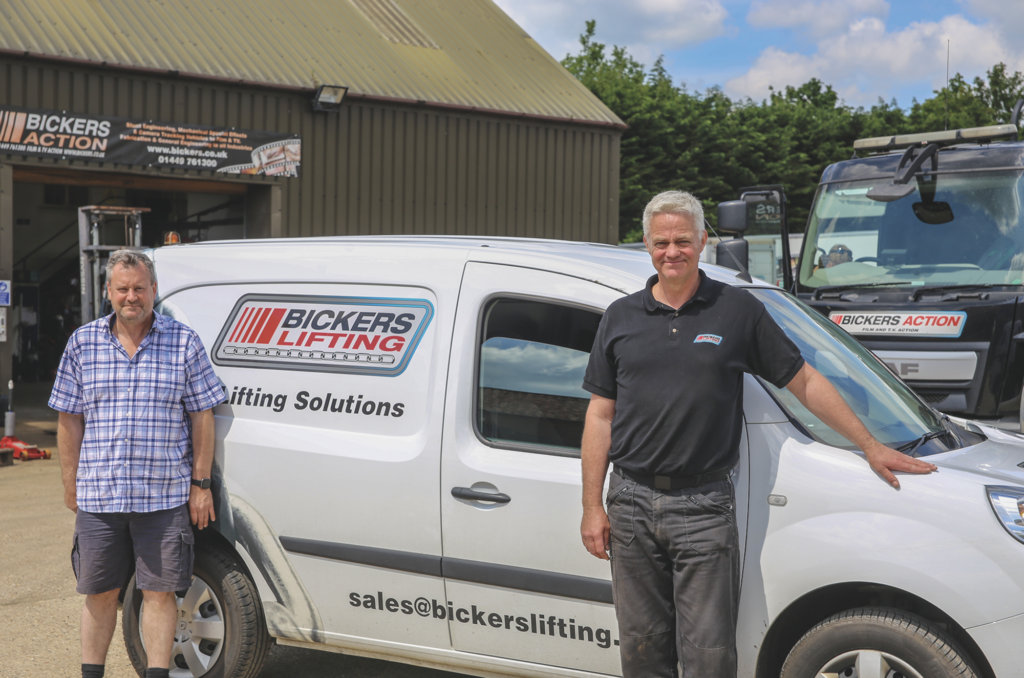
“There is greater awareness of the need for all lifting equipment to be tested regularly, to ensure it is safe to use,” explained Bickers Lifting general manager Steven Churchyard. “We are working with a growing number of agricultural machinery dealers, agricultural contractors and farmers using our service to ensure that equipment meets the required standards. This isn’t just about ticking forms to satisfy legislation. Knowing that lifting systems have been checked by an independent specialist is reassuring to owners and managers, and is part of their duty of care to anyone who might be affected if the equipment were to fail.”
Practical experience
Bickers Lifting is a division of Bickers Action – a family-owned business set up in 1976 to provide stunts, stunt equipment and special effects for the TV and film industries. Many dramatic action scenes featured in popular TV soaps, major feature films and TV adverts are created by Bickers, and part of the safety preparation involves meticulous attention to detail checking that equipment is safe to use, including straps, cables, harnesses, camera rigs and vehicles.
“We employ people with the expertise and qualifications to check it properly,” explained managing director Paul Bickers. “So it was logical to offer our services to local companies too.”
Business growth
Since Bickers Lifting was set up in 2008 the business has grown, and as well as providing on-site inspections of lifting equipment across the UK, it also stocks and supplies sundry items including cables, chains, straps, ropes, hooks, ratchets, tensioners and harnesses – all produced in Europe and available for collection or dispatch by carrier. “We stock premium products which we would be happy using ourselves,” continued Steven. “There are cheaper options – but it costs little extra to buy something which is good quality and fully certified, and which will probably last longer too.”
Farms and dealers
Onsite checks carried out at dealer and farm premises can include mobile machinery such as telehandlers or work platforms, workshop equipment such as gantries, hoists and vehicle ramps, and equipment carried by mobile workshop and service vans. “Lifting machinery such as handlers or cherry pickers should be examined annually. Lifting accessories and man- riding equipment as well as height safety equipment including man cages should be checked every six months,” explained Steven. “Working within the industry and using these products ourselves means we are realistic and practical, and where only components are worn we encourage a safe repair rather than insisting on a complete replacement which keeps prices down for our customers. While carrying out inspections, we often spot other equipment requiring checks too, but that customers aren’t aware comes under the legislation.”
Dealer’s experience
Ernest Doe & Sons Ltd has 18 depots across east and south-east England, and began using Bickers Lifting several years ago after changing from a national brand. “We weren’t happy with the service, so changed to a smaller family-owned business, and the Bickers Lifting team is excellent,” explained property and projects manager Alan Ringer. “Several potential suppliers were considered, but from when we first visited Bickers to discuss our requirements it was obvious that the people there care about what they do. The team is friendly and helpful and they listen to what we say and understand our requirements. The service is very good.”
All lifting equipment in workshops, yards and service vans is inspected, and an inventory is kept of everything checked so nothing is missed. “Inspections are mandatory – they are not a choice, and Bickers reminds us when inspections are due, then we issue an order number and leave it to them,” he added. “A full audit can be viewed on an online portal including the condition status of each item. If repairs or replacements are needed then these are highlighted, including straps and lifting harnesses as well as jacks and axle stands plus powered machinery. We buy lifting straps and other components from Bickers as they are good value for money, and the company adds them to our equipment list to maintain an accurate inventory. Equipment used on our farm is checked too; including less obvious items such as the bag lift on our fertiliser spreader which also needs inspecting. Certificates of inspection can be viewed through the portal, and when we have Health & Safety checks these are easily found. It’s reassuring to know that all our equipment is properly checked in line with Loler legislation and Puwer guidelines.”
Growing demand
Steven said that demand for his team’s services is growing, and most new business is through recommendation from existing customers, although there has also been interest from farmers buying groups keen to offer Bickers’ services to their members. “Our practical approach appeals. We will advise where alternative equipment might be more suitable, and we see our role as providing solutions rather than listing faults. We also suggest repairs rather than replacement where this is a safe option and will save the customer money. Repairs are completed in our own workshops, so when faults are found during inspections we bring the equipment back to our yard, repair and re-inspect it, then return it by carrier within just a few days.”
For more articles, read the latest Farmers Guide online, or sign up for the paper edition.