Case IH combine updates prove ideal for Kent farm
24th October 2019
Improved performance and new features of the latest Case IH Axial-Flow combines are expected to make it easier to establish and grow successful crops on a Romney Marsh farm. David
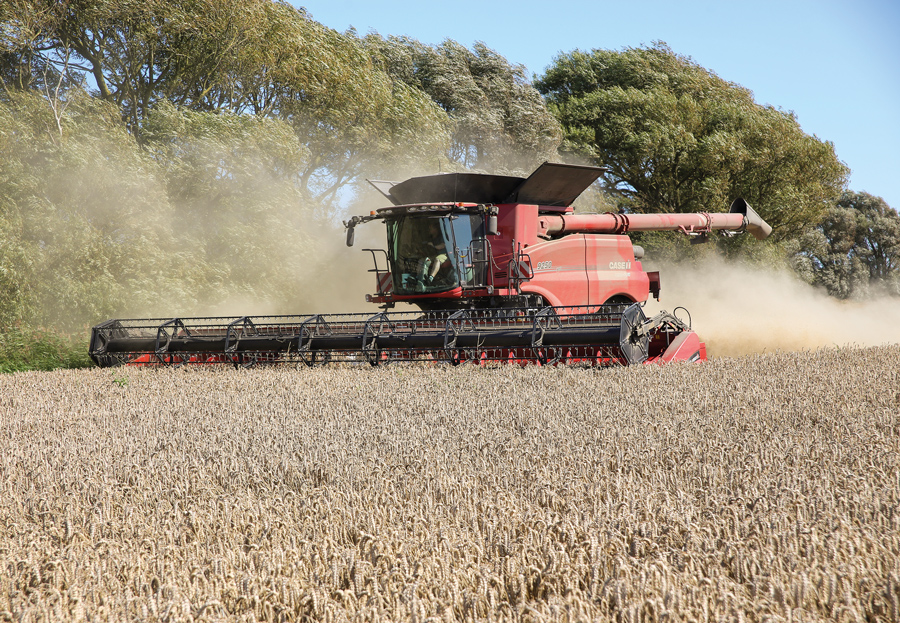
Improved performance and new features of the latest Case IH Axial-Flow combines are expected to make it easier to establish and grow successful crops on a Romney Marsh farm. David Williams reports.
“We regard harvest as the first cultivation of the subsequent crop,” commented Andrew Cragg who trades as Brooker Farms based at Newchurch in Kent. “Getting that first cultivation right means subsequent operations are easier, and crop establishment is more even.”
Andrew farms approximately 565ha of his own crops including wheat, spring barley, oilseed rape and combine peas, and collaborates with a neighbouring farm, which means the combine can also harvest an additional area of similar crops as well as oats.
All straw is chopped and most crops are established by minimum tillage although ploughing is currently preferred for peas following spring barley, due to peas’ dislike of compaction and the amount of fluffy straw on the surface. Oilseed rape is established direct into stubbles which requires a fine chop from the straw chopper.
The farm was an early adopter of control traffic farming (CTF) and Andrew says this has contributed to an improved soil structure and reduced the need for deep cultivation.
Six years ago, the farm upgraded to a 12.5m (40ft) header, for compatibility with its planned 12–24m CTF regime from a previous 9m (30ft) model. “We wanted to make the most of opportunities offered by CTF and there were limited options for those looking for 12m machines. Several manufacturers offered the header width needed and were keen to help, but the standard unloading augers remained too short which meant corn trailers would have to travel off the tramlines,” explained Andrew. “When we asked about a longer auger at that time the response was generally negative as it was thought the additional weight would be too much for the lower pivot mounting, except for Case IH which agreed to produce us an extended version covered by the full factory warranty. So, we moved away from our previous brand, and bought our first Axial Flow combine from local dealer Ernest Doe Power.”
With the wider header and the amount of straw that had to be processed by the standard straw chopper, residue was sometimes inadequately spread resulting in blocking of cultivators and drills. Andrew discussed the issue with his dealer and Case IH, and a Europe-wide solution was identified in the form of a Canadian-manufactured Redekop MAV chopper which was fitted by Ernest Doe Power. The Redekop attaches to the rear of the combine behind the standard chopper. Special blades produce a powerful air blast which helps blow chopped straw and chaff out to the sides more consistently than the standard chopper. It worked well, providing the solution Andrew needed.
Power and automation
With the Axial Flow 9230 five years old and due for replacement earlier this year, Andrew had no hesitation in investing in the latest 9250 Axial Flow, boasting additional power (634hp max) and extra automation to improve performance and work rates. It also had a larger 14,500-litre grain tank. The extra-long unloading auger was now available as an option on the standard price list and a Redekop MAV Xtra-chopping chopper, now factory fitted, was also selected, based on the performance of the previous unit.
Additional technology on the new Axial Flow includes AFS Harvest Command automation. This uses a network of 16 sensors throughout the machine to monitor performance and, using the information generated, 7 different settings are automatically adjusted to optimise performance based on the selected harvesting strategy.
Three levels of automation include a base version, which simply makes initial settings, but Andrew’s 9250 model has the top AFS Harvest Command system. This includes Feedrate Control which adjusts ground speed based on crop load to meet a desired outcome – performance to control losses; maximum throughput, or fixed throughput. The operator selects maximum engine and travel speeds, and performance is optimised within these limits.
Andrew’s new combine also has a clean grain camera which identifies broken grains and impurities for grain quality monitoring, plus sieve pressure sensors to monitor the cleaning load. These sense impending overloads, allowing the cleaning system to operate at maximum capacity, while also making adjustments when needed to prevent losses before they occur.
Four operating strategies:
Performance – which maximises harvesting rate until grain losses from the rotor or cleaning system exceed pre-set parameters.
Fixed throughput – a target throughput is maintained by varying the travel speed while settings are adjusted to minimise losses.
Maximum throughput – the combine operates up to the speed or power limit set by the operator while adjusting settings to minimise grain losses.
Grain quality mode – settings constantly adjust to maintain targeted grain quality and impurity levels, while also minimising losses.
Auto feed-rate control
Darren said automatic travel speed control is selected most of the time, as it offers advantages in variable conditions, where speed increases in response to areas of thinner crop, and reduces where crop is thicker. During previous harvests he has suffered from shoulder pain after long days using the joystick to vary travel speed, but he said this wasn’t an issue this harvest and puts this down to the automatic speed management which reduces joystick use.
“I usually set the limit at 120 per cent of rated engine power, but aim to maintain a work flow using 100–110 per cent,” he said. “The speed control system is responsive and in patches of very thick crop, forward travel can stop abruptly while the threshing system deals with a sudden influx – but average working speed when crop flow is more even is approximately 5.5–7.0kph, which is quite comfortable with the 12.5m header. When filling a trailer alongside I always select manual speed control though, as sudden changes could cause problems for the trailer drivers.”
Optimise throughput
A new feature on the latest Axial Flow is rotor vane adjustment from the cab allowing the operator, or AFS Harvest Command in automatic mode, to adjust threshing performance for the crop and conditions. Adjusting the vanes to a shallow angle means crop remains in the rotor for longer for aggressive threshing, while a steeper angle moves the crop through more quickly, allowing higher work rates.
Sieve adjustment can also be adjusted manually, or automatically through AFS Harvest Command, in response to information from the loss sensors, grain camera and sieve pressure sensors.
“I’m very impressed with the sample from the new combine,” commented Darren. “The previous model allowed me to set the crop type, and settings were applied automatically after which I checked the sample throughout the day and made fine adjustments, but this does everything itself. I had my preferred settings written down for each crop harvested by the previous Axial Flow and it’s encouraging that the new combine makes almost identical settings in automatic mode. I try to maintain the best sample possible for all crops as that reduces the work load for the grain store. The new combine achieves a better sample whether I make the settings manually, or allow the combine to make them automatically and this year the oilseed rape was the cleanest we have ever seen.”
Higher work rates
Darren has driven combines for 16 years since being employed by Brooker Farms and at the time he joined the team, 2 combines were operated, later reducing to 1. “I like having the automation available as being able to rely on the combine to look after the settings leaves me free to concentrate on what is happening around me, especially when working in difficult conditions or at the headlands,” he explained. “The feature I like most is the automatic speed control. It lets me push the combine to full capacity when conditions are right to get as much harvested as possible without having to worry about overloading the rotor and blocking it. Even though this harvest was generally dry, during the early stages we had few really good harvesting days. Heavy dews held us up in the mornings and light rain showers forced us to stop in the afternoons, so making the most of harvesting opportunities as crops were ready was essential.”
Better chop quality
The new combine’s factory-fitted Redekop straw chopper is also performing well. Andrew said similar performance to the previous retro-fit model was expected, and he wasn’t disappointed. In very windy conditions where spread width can be compromised the fine chop means that cultivator and drill performance are unlikely to be affected.
The new 12.5m header has performed well this season in all crops and Darren said the optional in-cab controlled operating angle adjustment proved worthwhile, improving performance in laid barley to the extent that only two lifters at each end of the table were needed, rather than a full set.
The new Axial Flow has an improved transmission with field and road modes and on-the-move 2-speed range selection. The tracks are also improved with better suspension, and Darren said that at 30kph maximum travel speed the ride is more comfortable.
The latest cab is similar to before but noticeably quieter and Darren said he believes this might be due to the new tracks with their reduced vibration and smoother ride.
Daily maintenance requirements are minimal and Darren commented that the fuel and Adblue filling points are conveniently located.
Soils improving
Since moving to CTF, soil condition has improved and fewer cultivations are needed. “We no longer feel the need to make all the fields brown,” explained Andrew. “This year we have invested in a 12m Dale Drill for crop establishment direct into stubbles where possible, and with the improved performance of the latest Redekop chopper this shouldn’t present any problems. Oilseed rape will be drilled straight into the chopped straw. A 12m Lemken Heliodor cultivator will create a light tilth for winter wheat after peas and oilseed rape, and for spring barley after winter wheat. Next year we will also trial this approach for a small area of peas. Tramlines remain largely untouched while the wider combine tracks are remedied with a special 2-legged Flat-lift.
“We also have a set of 12m rolls so almost all our field operations are now 12m CTF compatible, and although our target is to minimise field work through direct drilling where possible, we will be flexible in our approach when conditions require.”
Easy decision
Andrew said that as a result of the farm’s experience with the previous Axial Flow combine, including back-up from the team at Ernest Doe Power, no other combine brand was considered this time. “The Axial Flow is simple and reliable and we achieve an excellent grain sample with minimal losses.
“The back-up is excellent and we have also had a visit from a delegation of US-based Case IH representatives to find out how we are getting on with the machine. They were interested in our feedback and keen to know what we need for the future.”
Combine key to success
Andrew says a result of moving to 12m CTF is that the machinery used is large for the area farmed, but allows field operations to be carried out when conditions are optimal. “The main motivation for moving to CTF has been to improve soil condition and we have seen that during the gradual transition the land has become gradually easier to work, requiring less deep cultivation. Our new 12m drill not only fits the farm’s standard working width but it will also allow us to make the most of opportunities to use minimum cultivations where conditions allow. However, the main component of the 12m traffic regime is the combine. The new Axial Flow 9250 has an ideal header size, an unloading auger which allows trailers to remain in the tramlines and a straw chopper which chops finely and spreads effectively, which is crucial for our progression towards minimal tillage.
“This is why I always regard harvesting as the first cultivation of next year’s crop.”